روش HFW (جوش القایی فركانس بالا)
تولید لوله هایی با قطر خارجی 10 الی 610 میلیمتر با ضخامت 0.7 میلیمتر الی 20.6 میلیمتر از طول 4 متر الی 13 متر در یك پروسه پیوسته شامل فرمینگ، جوش القایی فركانس بالا، سایزینگ، برش و بسته بندی و اعمال آزمونهای غیر مخرب و مخرب (بر حسب نیاز خریدار) از مشخصات این روش تولید است.
دستور العملهای اجرایی در كارخانجات نورد و پروفیل ساوه بر اساس نكات فنی و الزامات تعیین شده در استانداردهای معتبر بین المللی (در زمینه مشخصات فنی مواد اولیه و فرآیند ساخت لوله و پروفیل) و مشخصات فنی خطوط تولید كارخانه تدوین گشته و در چهار گروه اصلی ذیل به كار گرفته می شوند :
استانداردهای ورق های نوردی طبق : DIN 1623-1 برای ورقهای سرد روغنی، DIN EN 10025 و API 5L برای ورقهای گرم.
استانداردهای لوله های آب و گاز طبق : ISIRI 3360، ISIRI 3574 ، API 5L، BS 10255 , AWWA C200
استانداردهای كنترل كیفیت گالوانیزاسیون طبق : DIN EN 10240 / DIN 2444
استاندارد قوطی و لوله های صنعتی و ساختمانی طبق : EN 10219-2 / DIN 10305
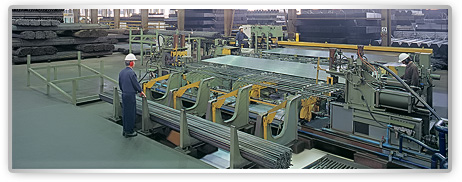
.
فاز 1 تولید
تولید لوله درزجوش به روش (Electrical – Resistance welding) ERW، با شكل دهی سرد (Cold Forming) نوارهای بریده شده از ورق های فولادی (Hot rolled) نورد گرم یا (Cold rolled) نورد سرد با پهنایی به اندازه محیط لوله مورد نظر در فاصله قالبهای دستگاه لوله سازی مرحله به مرحله از حالت مسطح به مدور شروع می شود. آنگاه دستگاه جوش القایی با فركانس بالا (High Frequency Induction) دو لبه نوار بهم رسیده را جوش داده و لوله ساخته می شود. سطح خارجی لوله در ناحیه جوش براده برداری شده و امكان براده برداری سطح داخلی هم وجود دارد. سپس برش محصول به طول های مختلف بنا به سفارش مشتری، آزمایشات مخرب و غیر مخرب جهت كنترل كیفیت محصول تولیدی بسته به استاندارد و سفارش انجام می پذیرد.
این فاز از كارخانه امكان تولید لوله با قطر خارجی 10 میلیمتر الی 168 میلیمتر با دستگاههای مدرنی كه قادر به تولید انواع لوله، قوطی و مقاطع مختلف صنعتی و ساختمانی، لوله های آب و گاز با سرعت 160 متر بر دقیقه می باشند نصب و مورد بهره برداری قرار گرفته است. همچنین در این كارگاه انواع پروفیلهای باز مثل ناودانی، نبشی، زهوار و قابهای درب با روش تولید مشابه تولید و تحت استاندارد و طبق نظر مشتری قابل تولید می باشد.
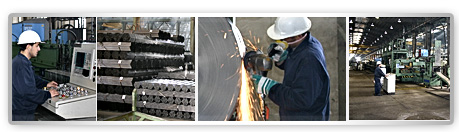
.
فاز 2 تولید
به منظور جلوگیری از خوردگی لوله های آب، گالوانیزه كردن گرم لوله ها در فاز 2 كارخانه که لوله هایی از قطر خارجی 21 تا 60 میلیمتر تولید می شود امکان تولید لوله و قوطی جهت مصارف مختلف وجود داشته که از سایز 19.5 تا 610 میلیمتر و همچنین گالوانیزه قوطی از سایز 20*20 تا 120*120 انجام می شود .
در این كارگاه روش Hot Deep Galvanizing به شرح ذیل انجام می پذیرد.
— ابتدا لوله های تولیدی طبق استاندارد های مجاز تولید و به واحد Pickling منتقل می شوند تا برای جذب بهتر پوشش فلز روی و گالوانیزه شدن آماده سازی شوند. در این مكان ابتدا لوله ها چربیگیری و سپس زنگ زدایی شده و به محلول Flux آغشته می شود. این محلول امكان نفوذ بهتر روی در سطح فولادی لوله را بوجود می آورد.
— لوله های آغشته به ماده فلاكس به دستگاه گالوانیزه منتقل شده و ابتدا در كوره پیشگرم تا دمای Ċ120 حرارت داده می شوند و پس از خشك شدن سطحی بداخل وان روی مذاب هدایت و در دمای Ċ450 و به مدت 1 دقیقه غوطه ور شده و به سرعت از آن خارج می گردند. بلافاصله بوسیله دمش هوا و بخار مازاد فلز روی سطوح خارجی و داخلی آن پاك شده و به منظور جلوگیری از تشكیل آلیاژ فلز روی و آهن بداخل آب سرد فرو برده می شوند.
— طبق استاندارد و سفارش مشتری انتهای لوله های گالوانیزه دنده شده و با درپوش پلاستیكی رنگی كه به منظور حفاظت از سطوح دنده ها و شناسایی آن نصب می شود پوشش می شود.
— مشخصات محصول تولیدی، استاندارد تولید و نام كارخانه بوسیله دستگاه Inkjet Marker روی لوله ثبت شده و سپس بسته بندی و به انبار محصول منتقل می گردند تا طبق سفارش مشتری بارگیری و حمل شوند.
.
فاز 3 تولید
در فاز 3 كارخانه كه لوله هایی از قطر خارجی60mm تا 610mm و تا ضخامت 20mm تولید می شوند امكان تولید لوله های گاز و قوطی های سنگین جهت مصارف ویژه وجود دارد.
1- مواد اولیه ورودی به كارخانه به عرض دلخواه (محیط لوله مورد سفارش) بریده شده و نوارهای بدست آمده به خطوط تولید منتقل می شوند. با توجه به گستردگی طیف تولید از نظر ضخامت و پهنای نوارهای فوق دستگاههای برش متعددی با برنامه ریزی دقیق هماهنگ می شوند.
2- نوارهای بریده شده در ابتدای خطوط تولید مجدداً باز شده و خط را تغذیه می نمایند به منظور تداوم تولید نوارهای مختلف سر به سر جوشكاری شده و امكان تولید سریع خطوط را بوجود می آورند.
3- استفاده از انباره (Accumulator) پیوستگی جریان تولید را تضمین می نماید.
4- به منظور بهبود كیفیت جوش لبه های نوار به خوبی توسط دستگاه (Edge milling) پرداخت شده و پس از شكل دهی توسط جوش HFW جوشكاری می شوند، سپس سطوح داخلی و خارجی جوش براده برداری می گردد.
5- كنترل كیفیت جوش به روش آلتراسونیك بلافاصله پس از براده برداری انجام می پذیرد و سپس به منظور بهبود كیفیت خط جوش در گروه های خاصی از فولادها عملیات (Annealing) به صورت اتوماتیك روی آن انجام شده و به آرامی با هوا خنك می شود.
6- مراحل تكمیلی لوله سازی شامل پلیسه گیری دو انتهای لوله ها طبق استانداردهای مرجع، تستهای غیر مخرب هیدرواستاتیك و آلتراسونیك و بازرسیهای مكرر حین تولید ضامن كیفیت محصولی است كه توسط بزرگترین كارخانه لوله سازی HFW خاورمیانه تولید می گردد.
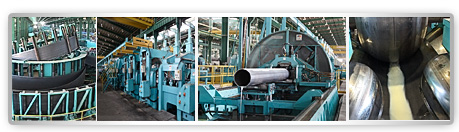